AIRCRAFT TRACTOR CAB
28th March 2020
CASE STUDY: Aircraft Tractor Cab
One-Stop Shop for Fully Integrated Composite Structures
A recent project working on the first composite cab for a ground support vehicle is a great example of COBRA’s Design and Development capabilities adding value for the end customer. When the Asia-based customer first approached COBRA, they were clear that they wanted a composite solution, but as metal fabricators, they didn’t have the in-house experience to develop the design for production.
COBRA Composite Structures was contacted in October 2017 and asked to assist with the rapid development of a composite cab for the customer’s Aircraft Tractor, which manoeuvres aircraft on the ground. Key requirements were a short project lead time and the supply of a fully finished solution – the target was to deliver 7 units in 2018 and 24 the following year.
CCS immediately began work on several iterations of the dimensions and styling for the new drivers’ cab and, with Composites Consulting Group (CCG), on composite engineering requirements for the new structures. Having signed off final designs in early 2018, tooling and production began with the first parts set to be delivered to the customer in March 2018.
Lightweight Composites for a Heavyweight Vehicle
Composites in transportation applications are often used to replace metal components for weight saving reasons but the 40 tonne Aircraft Tractor needs to maintain this massive weight to be able to push back large commercial aircraft.
The primary driver for composites in this application was to produce robust, low maintenance parts and to standardize the production assembly process. Previous metallic fabricated components were often built for each individual vehicle, resulting in slight dimensional tolerances that made it impossible to swap components between vehicles if required.
Precision moulded composite parts will speed up production and standardize the build process across the customer’s range of ground support vehicles.
That’s not to say lightweighting was off the agenda entirely – the new cab is significantly lighter than the original metallic parts and details such as door hinges can also be lightened due to the new lower operating loads. Composite panel enclosures at the rear of the vehicle are more than 50% lighter than the steel parts they replaced, improving health and safety and working conditions for maintenance technicians.
Rapid Start-up of Cost Effective Production Process
Using the dedicated Design and CNC resources at COBRA, CCS designed cost-effective master plugs for all the component tooling which were used to produce composite moulds. Finished parts for the new composite cab were infused using vinyl ester resins and glass fiber combination fabrics. Foam cores were incorporated in larger panel areas to increase panel stiffness and reduce weight, with these sandwich construction sections being manufactured in a single shot infusion process.
One of the challenges with this project was that customer wanted more than just a set of trimmed and painted composite parts. The fully finished drivers’ cabs were to be integrated with seating, instrumentation, lighting and other systems and then delivered direct to the customer’s production line.
COBRA has considerable experience of delivering complex automotive component sets and assemblies through its TS16949 certified-Cobra Advanced Composites (CAC) division, and CCS were able to use similar processes to coordinate local vendors and customer supplied items, meeting quality and delivery targets.
Looking Forward to a Composite Future in Airport Equipment
Following the success of this first composite project, the customer has commenced a design review of several other types of ground handling equipment in its range. The aim is for loaders, airplane steps, forklifts and baggage transfer trucks to all incorporate composite components in the very near future.
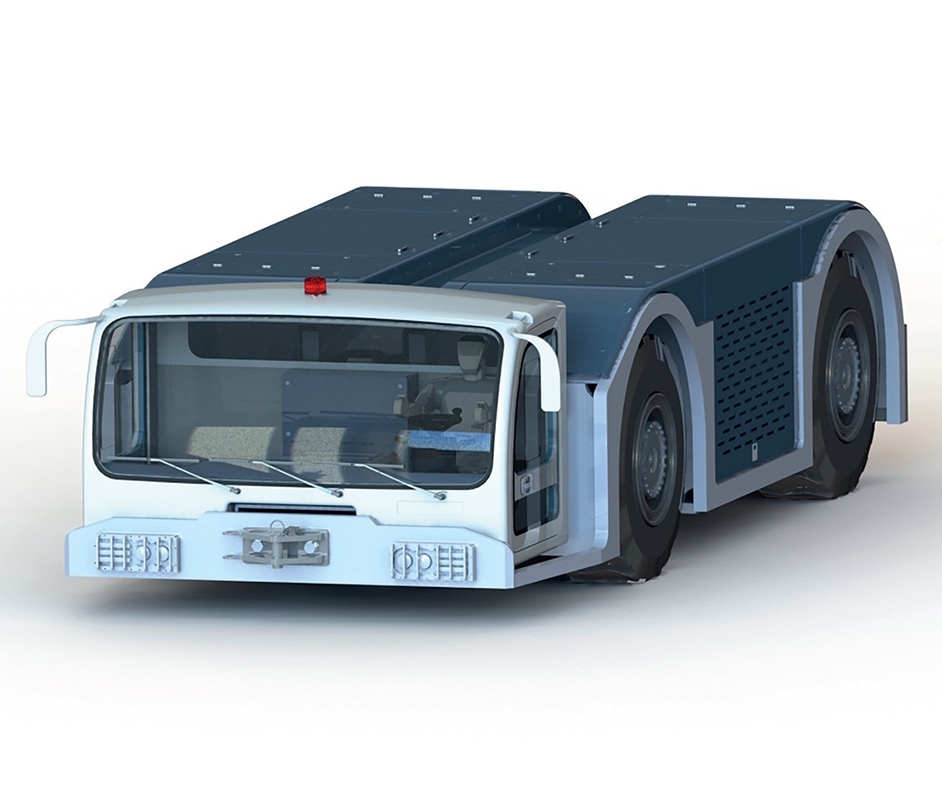