FLITE ELECTRIC FOILING SURFBOARD
28th March 2020
CASE STUDY: Flite Boards
Flite – next level foiling
The Flite electric foiling surfboard is taking surfing to new heights – and speeds. Although hydrofoils have been used on windsurf boards since the 1970s and 1980s, the last few decades have seen new materials, technologies and designs allow for this next level of development.
Powerful combination
COBRA has been involved with the project from the outset: from design and engineering, through prototyping of the boards, to foils and accessories. The team is now gearing up for production, since the range of Flite surfboards was launched into the market in late 2018.
Despite being highly engineered bits of kit, they are easy to customise, transport and set up, and offer the rider a noise-free and wake-free experience, with a zero-emission propulsion. They have a superyachtinfluenced shape, a unique deck pattern and are available in luxury finishes of black, white or ash wood veneer. And they reach 40kph. There are three models on offer: Fliteboard and Fliteboard PRO which are both of composite construction, and Fliteboard AIR, an inflatable model.
A carbon/Innegra prepreg EPS sandwich laminate was selected for the composite models, for maximum strength and stiffness at low weight, with each board weighing between 22-28kg depending on board, battery and wing choice.
Systems complexity
Mechanical performance, water tightness and durability were also important considerations at the development stage. The electric and electronic components are contained in a watertight thermoformed carbon battery box with a full carbon sandwich lid, which also enables the key components to be incorporated more easily into the inflatable board. In addition, an effective drainage system had to be put in place, and the creation of a strong connection between the battery box and the Bluetooth receiver was critical.
To resolve these issues, COBRA worked with Flite to produce several prototype boards in parallel, in addition to working on the thickness of the boards to accommodate the battery box, the engineering of the lid and the mast box for the foil.
Looking ahead
As technologies merge and customers become more demanding in a world where ‘nothing is impossible’, function and form are often equally important. Manufacturers must now demonstrate their versatility and breadth of expertise in being able to design and manufacture these more complex components, bringing together both performance and aesthetics, and show that anything is indeed possible. COBRA, with a focus on Strong, Light and Beautiful composite components is the ideal partner.
One-stop Shop
COBRA has also carried out developmental work on the foils and accessories for the Flite range. The foils will be manufactured in a dedicated area of the COBRA plant, with the deck pads and board bags being developed and manufactured by DSM in the separate soft goods manufacturing area.
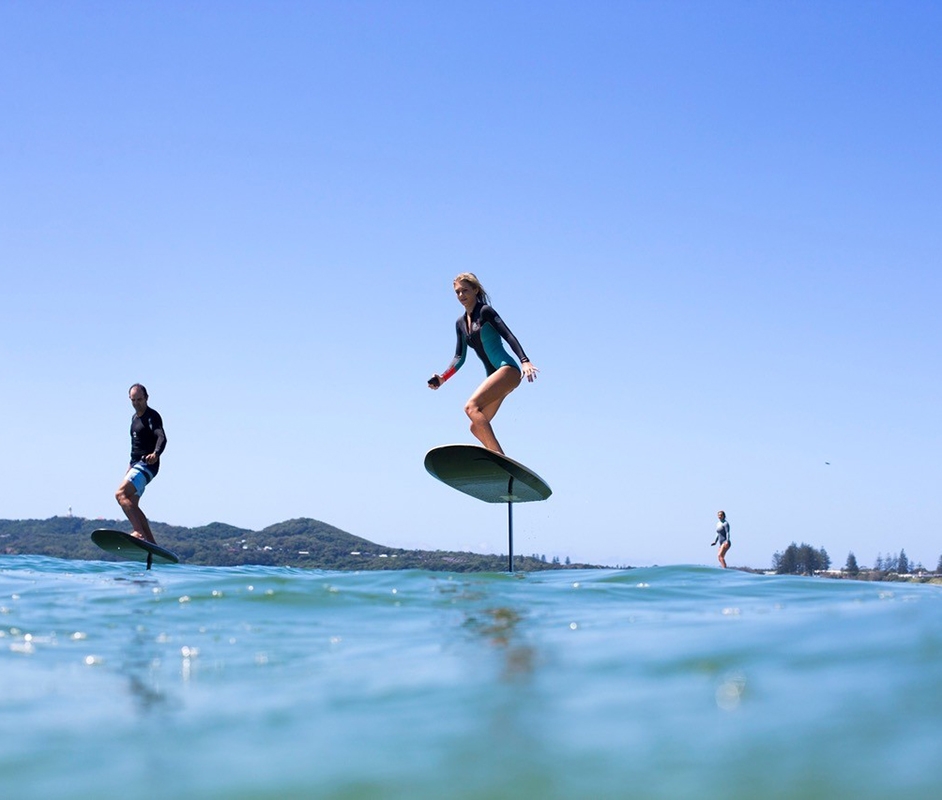