ARE Tahiti Composite Canoes
19th November 2020
COBRA’s latest watersports success story sees the group collaborate with leading outrigger canoe brand ARE Tahiti, building the company’s new canoe - or Va’a, as the traditional outrigger designs are known as in Tahiti.
ARE’s new OC-1 design – the ‘Mana’ - features a closed deck design where the paddler sits on top of the hull. The Mana is available in two versions; a lightweight 12kg and a weight optimized PRO version weighing only 9kg. Both models required the best in composite construction, a stunning final finish and a build rate that could keep up with a growing order book.
ARE was founded in 2004 by Yvon Fa’aite in Tahiti to manufacture a range of composite boats, components and canoes. The company is now owned and managed by former professional windsurfer Baptiste Gossein, who used to ride for JP Australia and Neil Pryde, enabling Yvon to focus on shop floor developments and production.
After Baptiste’s recovery from a serious, life-changing accident at the powerful surf break Teahupo’o, in September 2009, Baptiste and Yvon began to work together, officially joining forces in 2016, united by a strong passion for watersports and composites. Together, they began to move the ARE brand forwards and build on its strong reputation for build quality and performance on the water. As success brought more orders, they began to look for options to increase their output, specifically for the new OC-1 that would require a build rate of up to 50 canoes per month.
Baptiste and COBRA first started to discuss the new OC-1 design 3 years ago, but it was in 2020 after extensive R&D and prototyping in Tahiti that the project really moved into the production phase. The new design, needed the very best in lightweight composite construction.
As with most watersports’ projects at COBRA, a perfect CNC milled master model forms the basis of the mass production tooling. In this case, 2 sets of composite hull tooling were taken from the master plug allowing a build rate of up to 50 OC-1 canoes per month.
For the lay-up and construction process itself, COBRA’s decades of experience in high performance PVC foam sandwich windsurf board construction provided a solid starting point, with the final details coming from a new addition to the team. Richard Greene, legendary epoxy windsurf board builder and industry specialist, joined the team to set up and optimize the OC-1 production.
Having selected vacuum consolidated epoxy wet layup for the mix of woven and stitched biaxial reinforcements, COBRA are able to build down to the customer’s weight target with the absolute minimum of waste and additional consumables. Top and bottom sections of the hull are moulded separately then bonded together, with the smaller outrigger hull – known as the ama – produced in the same way. Prepreg carbon fibre and inhouse split mould tooling is used for the two Iakos, the two cross beams that join the ama to the main hull.
COBRA now builds both versions of the ARE OC-1, the hybrid version using an 80:20 mix of E-glass and carbon fibre reinforcement fabrics at around 12kg and the weight optimized full carbon version coming in at around 9kg. An in-mould applied finish coat is used for the hybrid OC-1 while the carbon fibre model benefits from COBRA’s ultra-light paint system.
COBRA’s one-stop-shop business model has become of a key part of their success in the watersports market. Not just a composite fabricator, they simplify customer logistics massively by offering a complete ready to paddle product, packed and available for shipment to customers and distributors around the globe. As well as the main composite structure, COBRA manufactures additional components including the carbon fibre rudder, EVA foam padded seat and protective bags for the hull, lakos and ama.
ARE have been delighted with the first COBRA built OC-1s, with the earliest boats going to Australia, followed by a batch of 36 boats for Tahiti.
“COBRA is able to provide mass production capability and rapid new model turnaround, as well as delivering consistently high quality. We are delighted with the first COBRA built OC-1s and have received exceptionally positive feedback from customers and racers” comments Baptiste Gossein.
The next project to enter production will be a V-1 canoe, longer and narrower and similar to the OC-1 but an open boat that the paddler sits inside, with no rudder or steering system, requiring more finesse to manage underway. Plans for the V-1 will also ensure an optimum light weight and high-quality mass production at COBRA.
The OC-1 outrigger canoe is a superb example of COBRA’s customer focused approach to production process development. By working closely with Baptiste and the ARE team, COBRA are able to provide mass production capability and rapid new model turnaround, as well as delivering consistently high quality. COBRA expects to see significant expansion in this sector over the next few years, with its production lines also perfectly set up for other types of canoes such as Australian racing surf skis and open water kayaks.
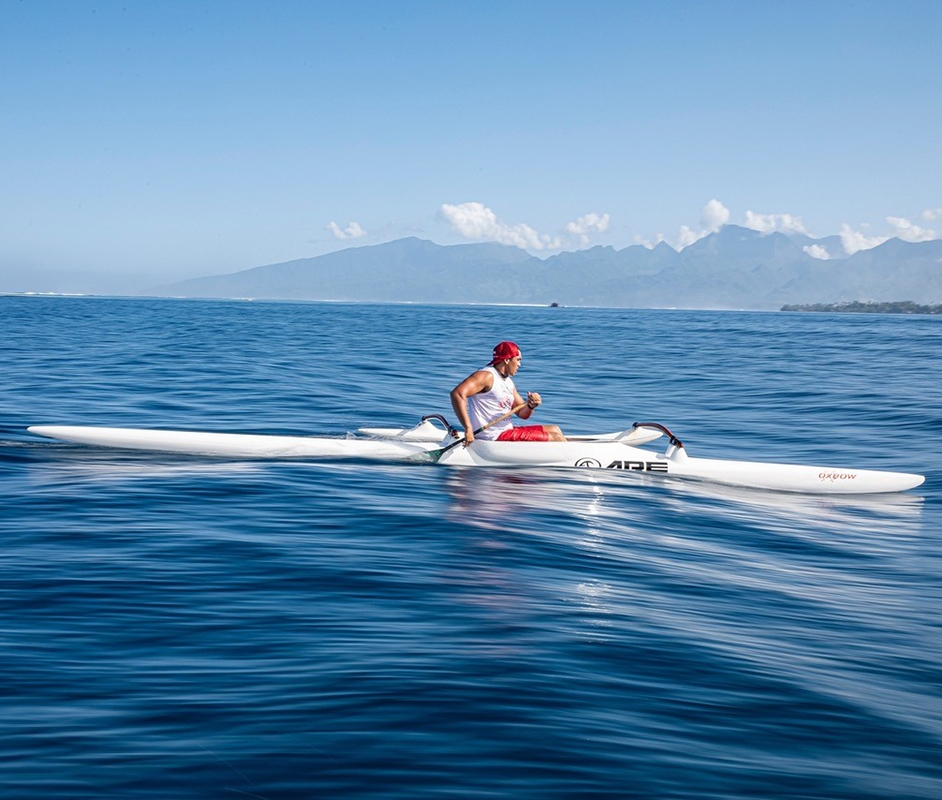