THE KING COBRA
6th September 2018
The King COBRA story begins in Europe in the summer of 1981, when Bert Morsbach and Rainer Ramelsberger meet Klaus Simmer, a young windsurfing pioneer passionate about developing the next generation of high performance windsurfing equipment.
Klaus had put his studies at the University of Munich on hold a year earlier and
relocated to Maui, Hawaii, where he began training under Barry Spanier as a sailmaker at Maui Sails.
It was also in Hawaii that Klaus and his brother Malte started to push their windsurfing equipment to the limits – and often beyond them – in the strong trade winds and pounding waves of Maui's North shore.
By the time he returned to Europe in 1981, Klaus was full of ideas and had already designed several custom boards and started to shape them himself. This made his meeting with Bert and Rainer at a windsurfing event on Italy's Lake Garda very timely indeed, opening the door for his ideas to be rapidly adapted to large-scale board production technology.
In the autumn of 1981, Klaus travelled to Thailand to join Bert, Rainer, Vorapant and the COBRA team and quickly got to work on his latest ideas for a new board that would plane quickly in the stronger breezes, but also perform well in lighter winds
PROTOTYPES
During his initial three-month stay with COBRA, prototypes were worked up and testing sessions held in Pattaya and Phuket, allowing Klaus to refine the original lines and finalise the King COBRA design.
At 12’ in length and with a volume of 220 litres, the King COBRA’s dimensions were similar to many other boards, but it was in the outline, rocker profile and underwater shape that Klaus was really able to work his magic.
By combining semi-displacement forward sections with a tri-plane planning surface in the tail, he succeeded in shaping a board that could change mode easily from upwind to downwind. With the mast track moved forward and daggerboard down, it went upwind well, and as the breeze increased riders could move the mast track back, fully retract the daggerboard and lock into the footstraps for fast but controllable planning. The rounded pintail shape in the tail was the first time such a detail had been used in a series production board.
CONSTRUCTION
With the shape defined it was time for COBRA to add production expertise to the mix
The King COBRA needed to be light, but it also needed to be tough. It was for this reason that an epoxy sandwich construction with hard PVC foam over an expanded polystyrene (EPS) core was selected. COBRA had pioneered this construction method and used it to great effect in the King COBRA, producing the lightest, stiffest and fastest production board available at the time.
Weighing only 35lbs (<16kg), the King COBRA offered performance simply not possible with a production board before. The King COBRA was something completely different to other boards of the time – a true all-round funboard
Whilst the team all believed they were really on to something with the new design and lightweight construction, some of most important feedback would come from the industry-leading test teams at the European windsurf magazines.
First tested by German Surf magazine in April 1982, the board was an immediate hit.
The King COBRA proved a breakthrough product for COBRA, establishing the company’s presence as a manufacturer of high performance windsurf boards and creating global visibility for the COBRA brand.
Suddenly, the company was selling as many boards as it could produce, but one disadvantage of the King COBRA’s popularity was that its shape was immediately copied by many other manufacturers – although none were able to replicate the advanced construction.
As a result, the King COBRA reigned supreme on the market for several years as the ultimate funboard.
“What I loved most about working with COBRA at the time, was that as a kid (just 22 years old), I thought I was on to something groundbreaking with my designs and ideas and I shared this burning desire to make the best possible gear with the owners, partners and top management” says Klaus Simmer today. “ They were just as passionate and committed as me and had the manufacturing technology to bring my ideas to fruition.”
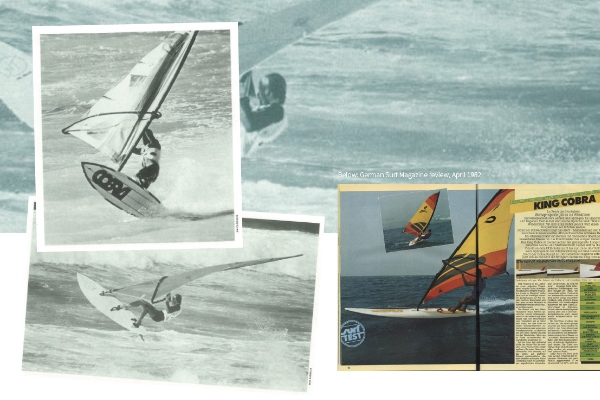