COMPOSITE PRODUCTS FOR THE ENTIRE SPECTRUM BY COBRA INTERNATIONAL AT CAMX 2018
9th October 2018
The entire composites spectrum is COBRA Internationals’ focus at CAMX this year with the company showcasing a range of composite products that span its full offering including carbon fibre components for the Automotive, Transportation, Marine, Water Sports and Luxury sectors.
From the CAC (COBRA Advanced Composites) team, now a crucial partner to many worldclass premium automotive and motorcycle manufacturers in Germany, Italy, Japan and the UK, parts on display for the transportation sector include examples of ultra-lightweight motorbike fairings and suspension arms. A full carbon sports car wheel which was designed, built and engineered at COBRA’s multi-million dollar automotive manufacturing and finishing plant in Chonburi will also be on the booth.
Foils take off with the latest composite technology.
With hydrofoils still creating a huge buzz in the water sports and marine worlds, designers are optimising foil shapes with the latest computer aided design tools and simulation techniques. The COBRA watersports team are the experts that bring these designs to life and they will display a number of hydrofoils, fins and foils designed and built for the Maui Fin Company (MFC) – the leading surf and windsurf fin specialist.
COBRA developed the first prototypes for MFC from scratch and helped to optimize construction methods, performance and the best attachment options for the wings.
The company uses multiple technologies to produce different options for prototyping, and then typically switches to resin transfer moulding (RTM) for series production to deliver repeatable, close tolerance parts that require minimal finishing on demoulding.
Bio-based epoxy resin systems are also becoming more common in foil production with COBRA leading the way in terms of switching major production volumes to more sustainable resin systems. Prepreg technology is also used when costly RTM tooling cannot be justified due to lower planned production runs, with COBRA able to tailor laminates to meet the performance or cost targets of each customer.
Lightweighting the latest furniture designs with a new full carbon chaise
Representing the work of the Design and Development department, COBRA’s internal hot house for new product development, a new Carbon Chaise prototype will also be on display having been built in partnership with customer Sutherland Furniture.
One of two prototypes, COBRA’s D&D team led the cooperation in terms of design, material sourcing, engineering and production to create a new modern take on the traditional chaise seat design that combines a full carbon structure with a waterproof textile net that is also created by COBRA. A full case study will be available at the show.
The full COBRA team will be available to discuss strong, light and beautiful composites at the show on Booth F79.
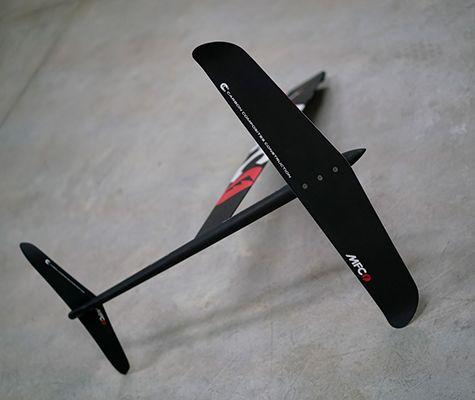